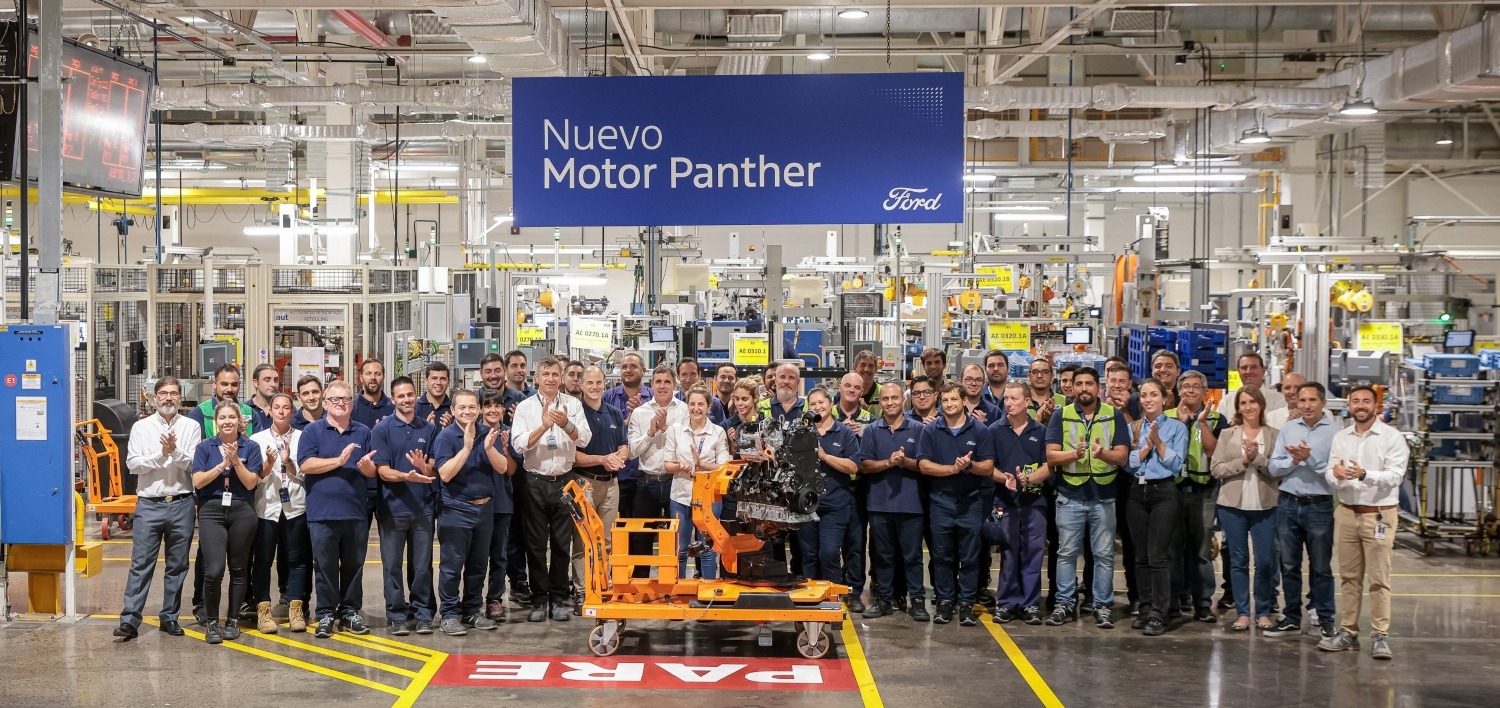
Meses después de la inauguración de la totalmente renovada planta de motores dentro del centro industrial de General Pacheco, donde desde el año pasado comenzó a fabricarse el propulsor turbodiesel Lion 3.0 V6, ahora Ford Argentina anunció que inició la producción del Panther 2.0 de 170 CV, que formaba parte de los planes de la compañía con una inversión de U$S 80 millones.
En este caso, se trata del motor turbodiesel de 4 cilindros en línea y 2.0 litros, que entrega 170 CV y 405 Nm de torque, que junto con el Lion V6 representan más del 80% de las versiones y de las ventas de la pick up mediana, que viene logrando un importante crecimiento en su segmento y también en las exportaciones. El propulsor Panther 2.0 biturbo de 210 CV y 500 Nm de par continuará llegando importado desde India.
Planta Pacheco celebró en 2024 su 63º aniversario y el sector de motores es casi tan antiguo como la propia fábrica: de su línea de producción salieron propulsores tan icónicos como los del Falcon o la F-100 y más recientemente el Puma 3.2 TDCi de la anterior generación de la Ranger. Sin embargo, para la renovada pick up fue necesaria una renovación casi total –según los directivos, sólo se mantuvo el piso, techo y las paredes-, ya que se incorporaron maquinarias, robots y tecnología de última generación siguiendo el concepto de manufactura 4.0, que ya se aplica en otras áreas del complejo industrial, agregando un alto nivel de automatización, conectividad y sustentabilidad, permitiendo además el monitoreo constante de cada etapa del proceso de fabricación, lo que contribuye a garantizar la máxima calidad y eficiencia.
La renovada planta de motores cuenta con una capacidad instalada para producir 82.000 impulsores al año en dos turnos y fue desarrollada con la participación activa de los equipos de ingeniería de Argentina y Brasil. Su sistema inteligente de gestión de calidad utiliza más de 2.000 sensores y 50 cámaras para monitorear motores y componentes a lo largo del proceso. Las 129 estaciones de trabajo cuentan con control automático de tareas, incluido un sistema inteligente de ajuste de tornillos. También fueron diseñados para optimizar la ergonomía y la comodidad de los operadores, quienes han recibido más de 5.000 horas de capacitación. El ambiente de presión positiva y los sistemas inteligentes de aire acondicionado e iluminación Led contribuyen al bienestar y la productividad.