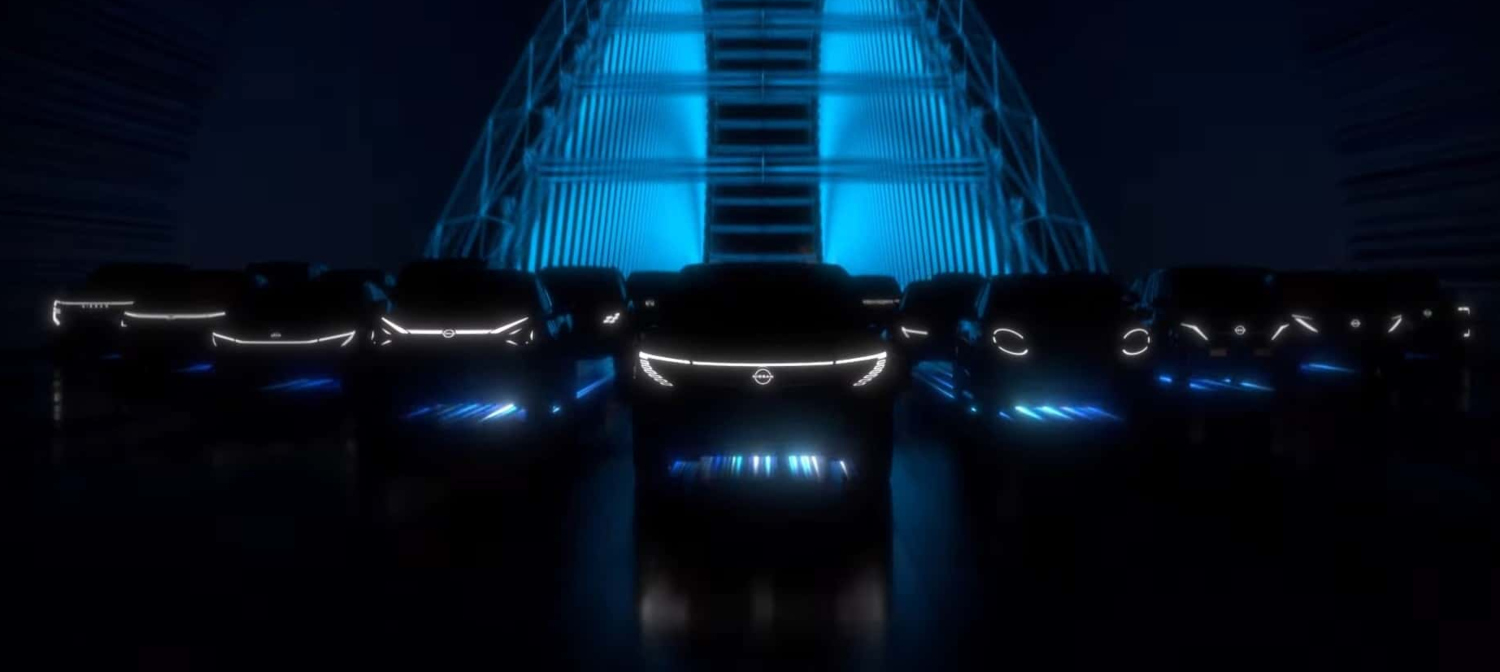
Aunque sus competidoras japonesas avanzan a un paso más lento en su camino hacia la electrificación total, Nissan sí está decidida a acelerar la transición. Sin embargo, al igual que el resto de los fabricantes, el gran desafío es lograr que sean accesibles para el público en general y aumentar su autonomía. Para ello, la firma nipona está trabajando en dos pilares: su sistema de producción y la fabricación de sus propias baterías.
Así lo reveló el CEO de la firma nipona, Makoto Uchida, como parte de su plan The Arc que, como señalamos en otros artículos, tendrá importancia global y se enfocará en las necesidades de cada región. A nivel general y en especial en el caso de los eléctricos, el ejecutivo indicó: “Deberemos cambiar la forma en la que planificamos, desarrollamos, fabricamos y vendemos automóviles”.
Para ello, seguirá el ejemplo de Tesla, introduciendo el método de fabricación conocido como gigacasting, que consiste en el uso de grandes máquinas que funden secciones enteras del bastidor de un vehículo en un solo paso. En lugar de unir numerosas piezas de acero estampado soldándolas entre sí, el gigacasting permitirá reducir los costes de producción en un 10% gracias a la reducción de tiempos, mano de obra y equipo. Para implementarlo, la compañía utilizará máquinas con unas 6.000 toneladas de fuerza para dar forma a la nueva generación de vehículos eléctricos que lleguen a partir del 2027.
Al respecto, Hideyuki Sakamoto, vicepresidente ejecutivo de fabricación y gestión de la cadena de suministro en Nissan, afirmó: “Hemos estado utilizando tableros de fundición para piezas estructurales de aire acondicionado frontal en nuestra planta de Tochigi durante más de 10 años. Tenemos bastante experiencia en la fundición de estructuras de automóviles”. Con estas mejoras, la marca buscará igualar el precio de los vehículos con motor de combustión con los eléctricos.
Eso no es todo. El segundo pilar es igual o aún más importante: para que un EV sea accesible, las baterías son clave y en ese sentido, Nissan planea desarrollar y producir sus propias baterías de estado sólido, que prometen marcar un punto de inflexión en los autos eléctricos ya que contarían con el doble de densidad energética, cargas mucho más rápidas y seguras, así como una vida útil mayor.
Al fabricarlas en gran cantidad, se ganará en economía de escala, abaratando sus costos. Ahí entra en juego la planta piloto de Yokohama, que Nissan está terminando de construir y que comenzaría a operar el año que viene. En una primera etapa de pruebas tendrá un volumen de producción de unas 1.000 a 2.000 unidades, iniciando la fabricación en serie para 2028, impulsada además por el lanzamiento de 19 vehículos eléctricos hacia el final de la década.