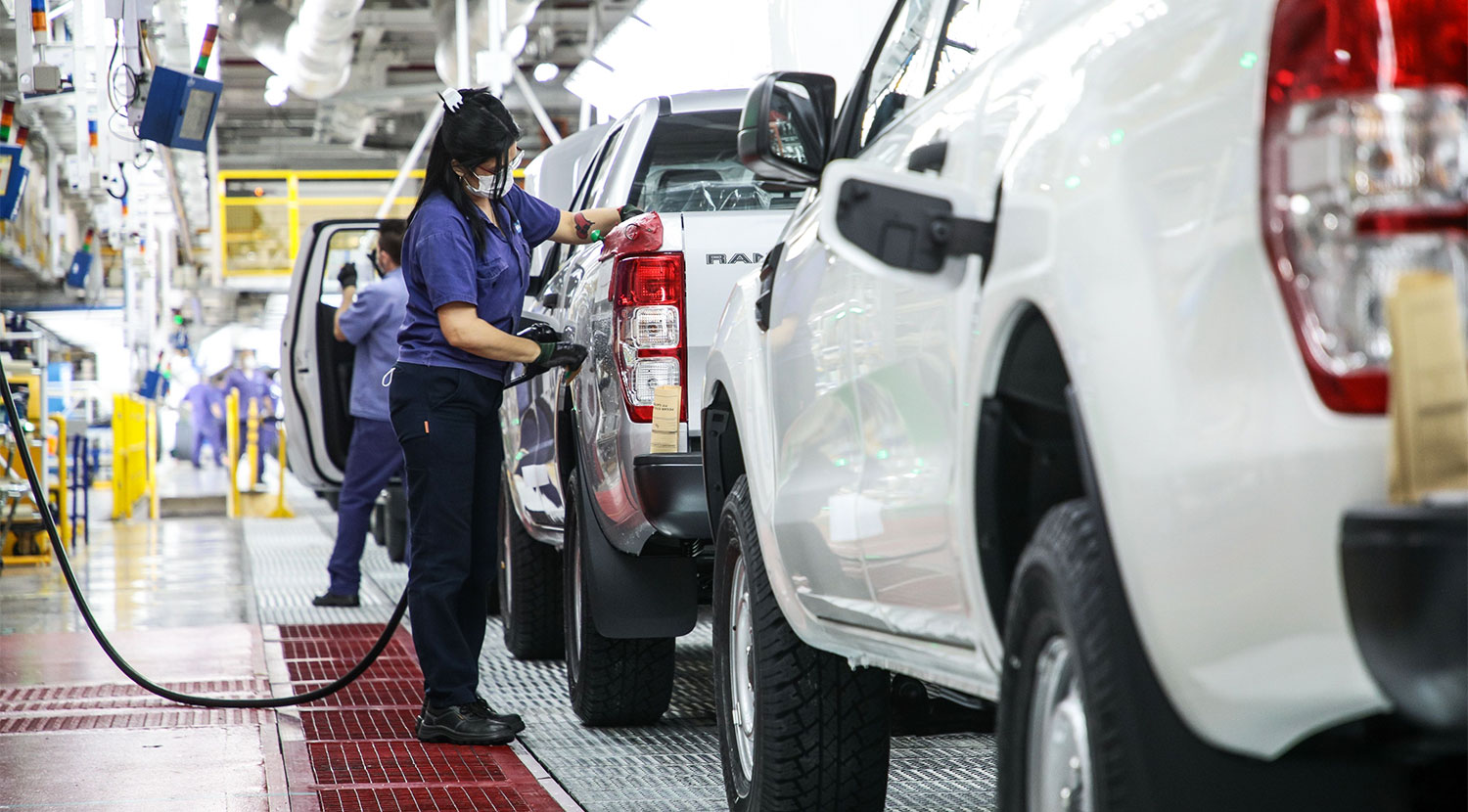
El pasado miércoles Ford Argentina realizó un reunión de prensa con casi un centenar de periodistas de Brasil, Perú y Argentina, de modo de mostrar lo que la marca realizó en la transformación de la Planta de Pacheco para producir la Nueva Ranger. De esta manera la marca de Pacheco anunció que comenzó con las pruebas para fabricar la nueva generación de pick up, que se lanzará durante el segundo semestre de este año.
En el evento estuvieron presentes Martín Galdeano, Presidente y CEO de Ford Argentina; Rogelio Goldfard, Vice-Presidente de Ford América del Sur; Alex Machado, Director de Desarrollo de Producto; Carlos Galmarini, Director de Asuntos Públicos y Comunicaciones Ford Argentina; Sebastián Trotta, Director de Ventas y Marketing Ford Argentina; Gastón Vainer, Gerente de lanzamiento e Ingeniería Industrial Planta de Pacheco; Osvaldo Santi, Gerente de Comunicaciones Ford Argentina y Francisco Molina Pico, Ford Perú.
En la presentación el Presidente de Ford Argentina afirmó «Ford tiene a nivel global una estrategia construida sobre la fortaleza de las Pick Ups, SUVs y Vehículos Comerciales, incorporando componentes de electrificación, tecnología y conectividad a sus vehículos con una estrategia muy clara para liderar la transformación de la industria. En este contexto la Planta de Pacheco tiene un rol muy importante porque abastece a la región con la producción de la pick up Ranger, siendo la calidad un pilar para que los clientes elijan este vehículo«.
Es por ello que para tener competitividad en costos y calidad la marca del óvalo invirtió con lo último en nivel de tecnología y que es comparable a otras plantas de Ford en el mundo. Desde la marca apuntan que el diseño está enfocado en la satisfacción de los clientes, que exigen y esperan cada vez más, es por eso que la calidad es parte fundamental para la fabricación de la nueva Ranger. Se invirtieron 660 millones de dólares, de los cuales el 30% se utilizó para el desarrollo de autopartistas a nivel regional.
Martín Galdeano dejó bien en claro que la nueva Ranger tiene un nivel de tecnología, confort, performance y seguridad que no es de su segmento y que se realizó la transformación de la planta para producir la mejor Ranger de la historia. Gracias a la incorporación de tecnología de manufactura 4.0, Pacheco es ahora una planta digitalizada y conectada, donde la información está disponible en tiempo real, jugando un papel fundamental para el aseguramiento de la calidad y productividad.
Ya yendo de lleno a lo que es la modernizada industria, se ubica sobre un predio de 1 millón de metros cuadrados de las cuales 250.000 m2 son cubiertos que incluyen áreas productivas estampado, carrocería, pintura y montaje final, además de la planta de motores, áreas administrativas y la Escuela Técnica Henry Ford, entre otros. La factoría de Pacheco es un centro de producción integral ya que en él se estampan las piezas de las carrocerías, para armar el body mediante procesos de soldado y luego pasan al área de pintura y montaje final; saliendo la pick up totalmente armada; trabajando en ella 3.500 colaboradores.
Con todos los cambios que se realizaron la marca tendrá una capacidad productiva de 110.000 vehículos que lógicamente tendrá una rampa ascendente de producción y que estiman que el 70% se exporte a otros países de la región, habiendo incorporado el año pasado mercados como República Dominicana, Guatemala y Panamá.
Recorrimos las áreas de estampado, soldado y montaje experimentando una planta completamente nueva conectada y de ultima generación, asombrándonos del nivel de cambio.
Sabemos que la diferencia entre un automóvil y una pick up es que los primeros son monocasco mientras los vehículos comerciales poseen chasis. Para fabricar las pick ups se arman con una carrocería (caja y cabina) donde el foco fundamental para garantizar la calidad están centrados en la estabilidad dimensional. Luego esta cabina irá montada sobre el chasis donde se va a ubicar el motor, suspension, caja, etc y ese chasis va a ser el corazón de la camioneta. Es por eso que la principal característica que tiene que tener ese chasis son los ajustes de cada una de las fijaciones; por lo que hay que asegurar la calidad con los torques de cada uno de los bulones.
En el área de estampado se instaló una nueva linea de prensas de alta velocidad, una imponente instalación de 59 metros de largo x 12 metros de ancho de última generación y como las que se utilizan a nivel mundial, siendo cuatro veces más rápida que la actual (1.800 piezas/hora), con mayor capacidad de embutido y mayor tonelaje alcanzando las 2.500 tn, permitiendo una mayor calidad de las piezas. Además por su denominación Tandem XL permite estampar piezas de gran tamaño e incluso dos a la vez.
Para darnos una idea del tamaño de esta linea de estampado basta decir que para transportarla fueron necesarios 140 semiacoplados de 14 metros. Por otra parte se debió subir el techo 6 metros ya que el anterior era de 12 de manera que pudieran entrar la lineas de prensas. Además se tuvo que hacer una fosa para poder instalarla que tiene la misma altura de la prensa hacia abajo, utilizándose 900 m3 de hormigón y 70 toneladas de hierro.
Otras de las cualidades que tiene esta linea de estampado es el reemplazo de matrices que ahora se puede realizar en solo 4 minutos cuando antes eran necesarios 23 minutos. Como ya dijimos en varias oportunidades la calidad será uno de los pilares de la nueva Ranger es por eso que instaló un scanner 3D denominado Blue Line Scan paras mejorar la capacidad de control de las piezas estampadas, teniendo una precisión del orden de las centésimas.
En la planta de carrocerias se instalaron 318 robots, triplicando la cantidad que se tenían; realizándose el 95% de los puntos de soldadura mediante estos dispositivos. Al disponer de robots la capacidad de soldadura aumentó porque además de ser automáticos y tener una mayor repetitvidad tiene un control adaptativo de soldadura; que monitorea cómo está la soldadura y en función de cómo está va a justando sus parámetros. De esa manera nos garantiza que cada punto que se da, está en la posición correctas y tenga el nivel de temperatura que requiere para una soldadura adecuada.
Adicionalmente se trabaja sobre localizadores geométricos para garantizar la estabilidad dimensional. Son sensores de presencia, láser, cámara, etc; que monitorean la linea para garantizar que se está produciendo de acuerdo a las especificaciones. Si hubiera algún problema da aviso y se sube un reclamos al sistema de gestión y da los avisos para intervenir.
En el área de Pintura, además de la tecnologia “Alto Sólidos”, que brinda acabados de mayor calidad, mayor resistencia y es más amigable con el medio ambiente, se implementó un nuevo almacén inteligente de secuenciado de cabinas -conectado en línea con los proveedores Just in time- que permite maximizar la productividad de la planta y aumentar la capacidad del sector.
A lo largo de las líneas de producción, se distribuyen más de 1,000 cámaras, sensores y dispositivos que monitorean múltiples parámetros en tiempo real y usan inteligencia artificial para garantizar el alto patrón de calidad del producto final. Otras novedades incluyen un sistema automático de control de herramientas de torque, un sofisticado sistema de escaneo 3D para el control dimensional de piezas y 81 dispositivos inteligentes para configuración y testeo de los más de 50 módulos electrónicos que gestionan el alto contenido tecnológico de la nueva pick-up mediana del óvalo.
La ergonomía, seguridad y bienestar de los colaboradores fue también una prioridad a la hora de planificar esta importante transformación. Entre otras acciones, fueron instalados manipuladores y brazos con sistema “zero-gravity” que permiten manipular piezas grandes y pesadas con mínimo esfuerzo, así como también sistemas de climatización inteligente. Los equipos recibieron más de 40,000 horas de entrenamiento, como parte del cambio de cultura y tecnológico que implica operar una planta 4.0, digital y conectada.
Se alargó la línea de montaje final que permite agregar complejidad a la planta y poder hacer distintos catálogos y versiones. También los operadores trabajan mucho más cómodos siendo otro factor fundamental para garantizar la calidad, no hay fosas y son espacios abiertos. Se instalaron 21 km de transportadores que ayudan a generar un mejor flujo en la planta e impacta en la capacidad de producir.
Como se ve hay un foco muy fuerte en la gestión de la planta, siendo cada vez más tecnológica, compleja y conectada con herramientas para gestionarla y controlar los torques de cada una de las unidades en cada una de las estaciones y de estas manera ofrecer a los clientes los productos y servicios que quieren y valoran a través de plataformas globales de próxima generación.
Tengo deseo que produscan un modelo 4×4 naftero