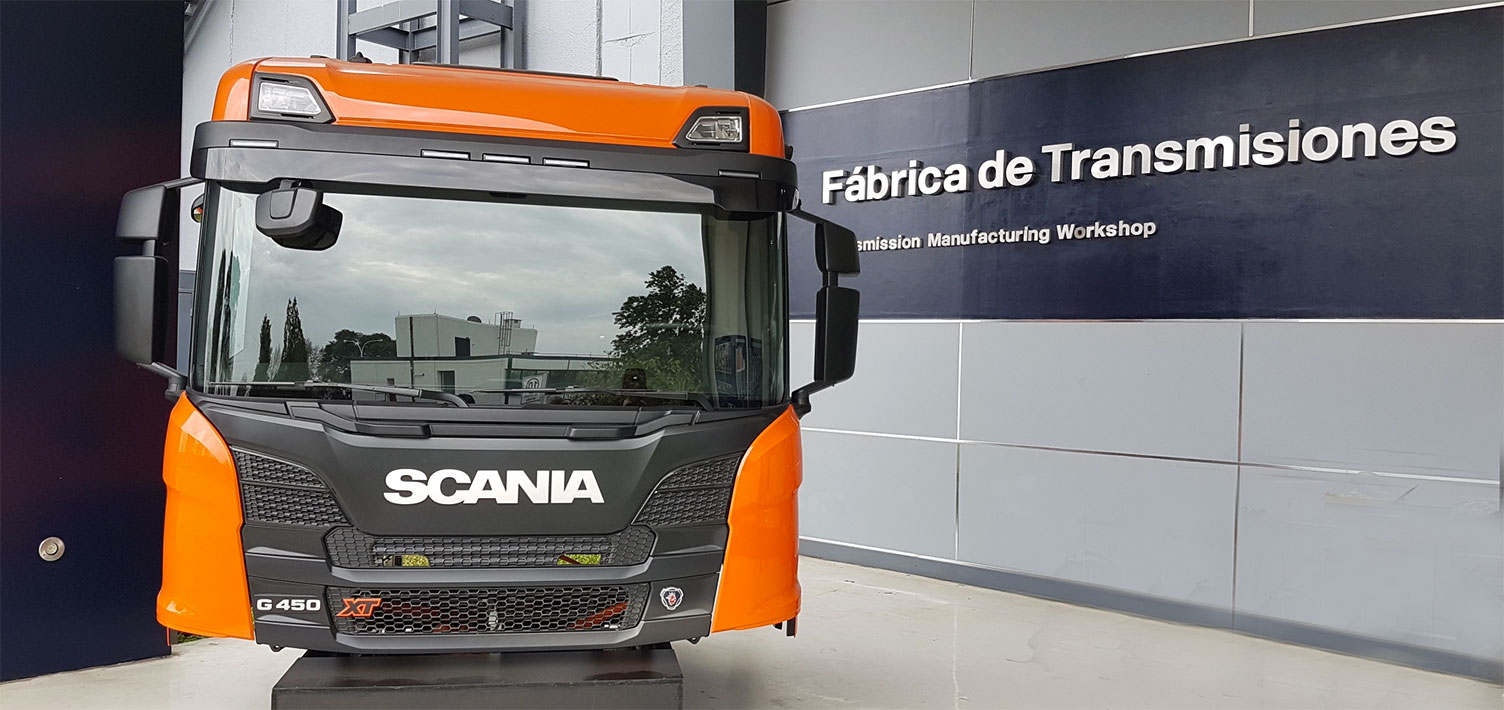
La Planta de Scania Argentina se encuentra ubicada en la Localidad de Colombres a pocos kilómetros de la Ciudad de San Miguel de Tucumán. Es una planta de última generación con el mejor nivel internacional, encontrándose totalmente integrada al sistema de producción global de la marca, que se encuentra pasando por un proceso de transformación junto a todo el sistema productivo con la nueva generación de camiones
Invitados por Scania Argentina visitamos la factoría que fue inaugurada el 26 de Marzo de 1976 contando con una superficie total de 230.000 m2 y un área cubierta de 41.000 m2 donde trabajan 540 empleados. En sus inicios fue diseñada para el montaje de camiones y la fabricación de cajas de velocidades. Hoy produce exclusivamente componentes de transmisión, caja y diferencial (ejes, sincronizados, corona y piñon, engranajes, carcazas de caja, mitad porta-coronas y palieres), que son elementos estratégicos y parte del sistema global de producción. Solo hay dos plantas de este tipo; una en nuestro país y la otra en Suecia, por lo que ambas disponen del mismos equipamiento y los mismos controles de calidad.
En la actualidad cuenta con once líneas de producción trabajando 540 empleados para producir 30.000 cajas y 40.000 diferenciales al año; en tres turnos para la producción de diferenciales y cuatro turnos para el proceso de tratamiento térmico, exportándose la totalidad de la fabricación a Brasil y Suecia, en una relación 83%/17%, estando la planta certificada con las normas ISO 9.000 y 14.000.
Una de las prioridades de la planta es la responsabilidad con el medio ambiente alineándose con los objetivos a nivel global de la compañía: Para el 2020 las 9 fábricas que tienen en el mundo deben utilizar energías limpias libres de fósil; para el 2020 reducir el 25% de desperdicios en la producción que no son reciclables, para 2025 que el 50% de los vehículos producidos sean con energías limpias y para el 2020 lograr un 33% de reducción de energía respecto al 2010.
Para cumplir estos objetivos se encuentran realizando el reemplazo de luminarias por iluminación de led, que no solo permiten un ahorro del 10% de energía sino que tienen una mayor vida útil. Por otra parte utilizan emulsiones sintéticas y de aceite biodegradable , que también permiten extender su vida útil en los procesos productivos, reduciendo el consumo de hidrocarburos durante la fabricación.
En cuanto a tratamiento de residuos: los aceites y virutas metálicas son reciclados en su totalidad, aprovechándolos en nuevos procesos productivos o convirtiéndolos en materiales reutilizables. El resto es enviado a plantas recicladoras de la provincia. También la fábrica posee su propia planta de tratamiento de efluentes cloacales e industriales, que permite que el agua pueda ser reutilizada para riego de cultivos y otros procesos productivos en la empresa.
Desde el año 2019 Scania comenzó con una inversión de 35 millones de dólares que se extenderá hasta el 2020 para el reemplazo de maquinaria que provienen de Estados Unidos, Japón, Alemania y de nuestro país y capacitación de sus operarios. Entre ellas se destaca las máquinas de corte en seco, una tecnología desarrollada en Estados Unidos que elimina la necesidad de utilizar fluidos de corte para refrigerar.
Realizamos una pequeña recorrida por la planta donde pudimos ver algunos de los trabajos que se realizan en ella. Nos explican que el material ingresa desde el proveedor en bruto pàra luego mecanizarse «en blando» (sin tratamiento térmico), para luego pasar por los hornos de tratamiento térmico para mejorar la dureza y resistencia y para finalizar con un mecanizado «en duro». Este último mecanizado se realizan ya que en el proceso de tratamiento térmico la pieza puede perder la forma geométrica y variar las magnitudes. Hay piezas como el sincronizado que no se les realiza mecanizado «en duro» ya que el temple se realiza en una prensa .
Otra de las máquina incorporadas a la línea de producción son las de rectificado de piñon y corona que mejora la tolerancia, permitiendo aumentar la resistencia un 25% incrementando la vida útil y reduciendo el nivel de ruido.
Las exigencias en calidad se podría decir que son extremas ya que se realizan con distintas metodologías desde calibre y micrómetros hasta dispositivos y máquinas de medición en ambiente controlado, de modo de asegurar que las piezas se fabriquen con la calidad requerida en cada punto del proceso. Solo para darse una idea la amplitud de los diámetros de los piñones es de 18 micrones y . recordar que el diámetro de un cabello varía entre 15 y 100 micrones.
Para el tratamiento térmico disponen de tres hornos que poseen una atmósfera de carbono llevando la piezas hasta los 930ºC para luego ser enfriadas bruscamente en aceite hasta los 60ºC, de modo de modificar la estructura molecular de la pieza y realizar un endurecimiento superficial. Estos hornos necesitan un mantenimiento anual que dura cuatro semanas y cada 10 años se reemplaza todo el revestimiento refractario.
Scania dispone de un proceso para los engranajes denominado Shot Peening, que permite aumentar la resistencia a la fatiga entre un 25 y 40%. El proceso se realiza impactando con pequeños cilindros (aunque se los llama bolillas) las piezas generando un estado tensional residual, permitiendo prolongar la vida de la pieza. Este proceso es muy utilizado en la industria aeronáutica.
Dentro del proceso de fabricación el transporte de piezas es uno de los procesos más críticos y controlados por el riesgo de no tener el material en el lugar necesario en el momento que hace falta, causando cuellos de botella que hacen descender la productividad. Es por ello que Scania utiliza los denominados AGV (vehículos de guiado automático), son vehículos totalmente eléctricos con carga automatizada de batería, que se mueven de forma autónoma transportando piezas sin necesidad que un operario los conduzca. Pero no solo permite optimizar la cadena productiva sino también protege al operario al no tener que cargar, descargar y transportar las piezas y finalmente reemplaza los autoelevadores que utilizan combustibles fósiles. Hoy la marca sueca de camiones cuenta con 10 AGV y a fin de años estiman llegar a los 30; con la particularidad que fueron 100% fabricados por los operarios.
La seguridad y la capacitación son partes importantes en este el proceso de fabricación, es por ello que Scania dispone de una sala para entrenamiento denominada PRS (Percepción, Riesgo, Seguridad, Salud y Medio Ambiente) de modo de asegurar que no haya accidentes y ver que cada persona pueda percibir el riesgo en el trabajo.
En capacitación dispone de un área llamnadaa STTA (Scania Tucuam Training Area) donde se capacita y entrena a los operarios en las tareas de producción, mantenimiento, calidad, manejo de herramientas, control y manejo de máquinas entre otros.
Es buenísimo leer este tipo de noticias. Saludos a todos.